Yesterday I had one of those moments of disappointment again, which one as an inventor unfortunately has again and again.
I read an article reporting that a patent had been filed for volumetric 3D printing. At first I was very disappointed, because I thought about it a few years ago.
I also presented my concept to a professor who was critical but interested.
But then I was able to come to terms with the disappointment and I was happy that I had a similar idea and I could see that 3D printing technology was evolving. I still have one or the other idea in my quiver or in my notebooks ?
Basically, my idea would still be feasible, since it differs a little from the patent. But the technological prerequisites far exceed my knowledge and skills, so that I cannot realize them myself anyway.
The idea of the patent (rough summary)
The idea is to fill a container with metal powder and compress it. The component is then melted together with one or more focusable electron beams. This has the advantage that it is possible to develop an algorithm that constructs the component in such a way that there is as little distortion as possible and one is free to control the construction in all 3 dimensions.
My idea
My idea differs primarily only in the way the energy beam is used. Electron beams were no real concept to me until now. I was looking for an energy source that could at least theoretically be focused and that could penetrate materials. Then I came across X-rays.
Description of the idea I documented in 2018:
While I was working on a low-cost SLS-3d-printer, I had several years ago this idea for a kind of volumetric-plastic-powder 3d-printer.
While watching SLS-printer and my own prototype working, I noticed, that most of the process time is needed for laying down each single layer.
Another Problem by the layer by layer approach is the Anisotropy of the final product in the Z-Axis, in which the layers are laid.
This idea is way out of my possibilities to realize in my lab. Thus, I’m publishing it and I hope to be involved somehow in any success, so that I can continue to finance my laboratory, ideas, dreams and family in the future.
The Idea
Instead of laying down each layer, there should be some prepared and compressed powder cartridges which you easily can load and unload from the machine.
To melt the powder into a model, we can’t use a laser, because we need to reach into the centre of the cartridge. But there are ways to focus and align x-ray-beams to bring the energy into the cartridge, to the point we need it.
And since, we can place the power in the cartridge anywhere we want, we can switch from the layer on top of layer modelling type (which leads to anisotropy) to an organic modelling type and eliminate the anisotropy problem which all current 3d-pringing processes have.
To speed up the process and have a more even thermal expansion and shrinking inside the cartridge, I would propose to use more than one beam at the same time to print the model. I also would recommend applying some “intelligent” Machine Learning Algorithms, maybe K-Nearest or some DL-Networks to find the fastest and most thermal problematic reducing paths for the beams.
Some facts about the idea:
Advantages:
- Anisotropy is eliminated with evolutionary algorithms
- Layering is eliminated
- Faster than Laser sintering
- High Density of Materials possible
- Uncomplicated Material handling
Disadvantages:
- Completely new process
- Maybe, needs basic research
project steps
- First prototype on a 4 axis gantry with a single source
- Second prototype on a single axis gantry with a single source which has a scanning head and a dynamic focus
- Third prototype on a fixed base with different sources or one source, that’s split up in different beams. Each source or beam has its own scanning head and dynamic focus mechanism
Here are some of my sketches:
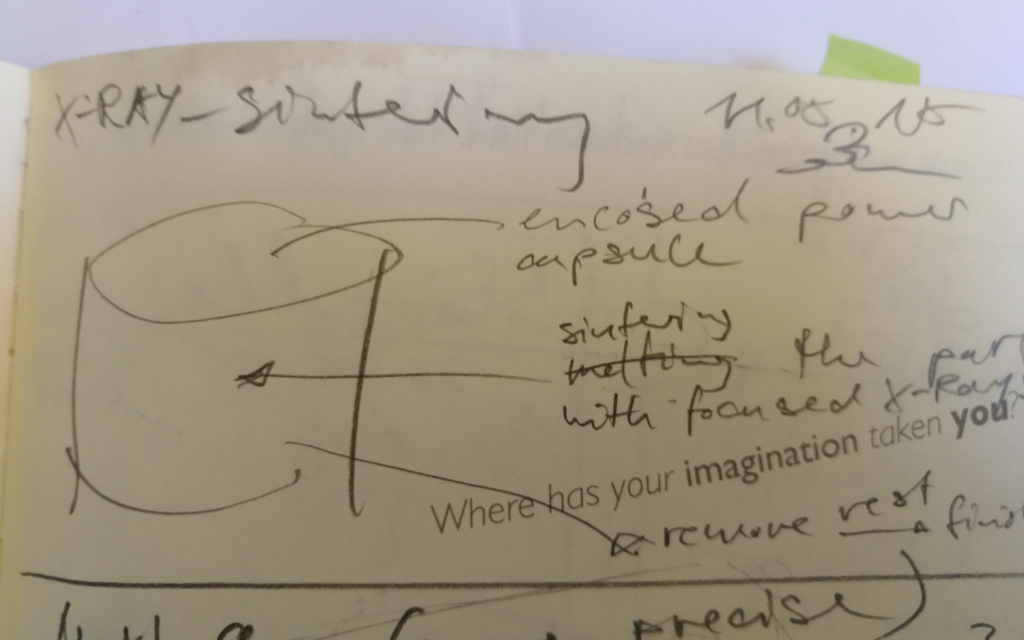

Links
- Article on 3Druck.com https://3druck.com/forschung/patent-fuer-metall-3d-druck-ohne-schichten-angemeldet-2078930/
- Article on 3dprintingindustry.com https://3dprintingindustry.com/news/patent-filed-for-metal-3d-printing-without-layers-147049/
- Link to patent: https://patentscope2.wipo.int/search/en/detail.jsf?docId=WO2018229085&tab=PCTBIBLIO&office=&prevFilter=%26fq%3DOF%3AWO&sortOption=Pub+Date+Desc&queryString=&recNum=1866&maxRec=3438409